by B Cantin | Jun 27, 2016 | Gemini 3D Printer
After getting the latest prototype of the Gemini 3D printer up and running I was dissatisfied with the assembly, implementation, appearance and performance of the overall system.
I starting playing around with some ideas in Sketchup by moving bits around and fiddling with the layouts and came to realize that I could eliminate several of the aluminum extrusions and reduce the overall materials cost as well as exterior size of the machine.
A few new parts came together really fast once I started reimagining the overall frame design
- New corner bracing – the first design did not work well, the second design worked better but turned out to not have the requisite strength or aesthetics I would have hoped for. Assembly was a chore to deal with if parts needed to be changed out. The new corner braces are a more traditional style but have been 3D printed in ABS with thick perimeters to make them strong and less brittle.
- From the new corner brace design I created a new 120mm fan mount with the AC plug and switch integrated as with the last prototype – however the part now forms a protective box around the live AC wiring and I have designed a fan duct to redirect the air vertically into a channel which will cover the power supply and direct the air towards the left corexy drive motor and extruder motor.
- With the new compact frame design I needed to come up with a new way of mounting the vertical smooth rods for the Z axis – I came up with a snap-fit connector which uses and M4 bolt to clamp the rod in place. By using these clamps I will be able to ensure correct and sturdy alignment of the linear axis is something that is easy to achieve. Disassembly and servicing the axis will be greatly simplified with these parts.
The new clamping system also permits the effector to move towards the back of the printer by over 20mm more than it could previously – this allows me to move the bed that much closer to the linear rails which reduces the lever/fulcrum effect of the moving platform.
- Some basic repositioning of the effector parts is also necessary – the flat aluminum stock which I used for the Rev 3 prototype is not stiff enough to prevent the X axis linear rail from sagging towards the centre which causes uneven contact with the bed across the width of the print area. I will be replacing this assembly with the one from the previous build where the linear rail was attached to a 3 sided aluminum channel, or potentially an L shaped channel for more rigidity.
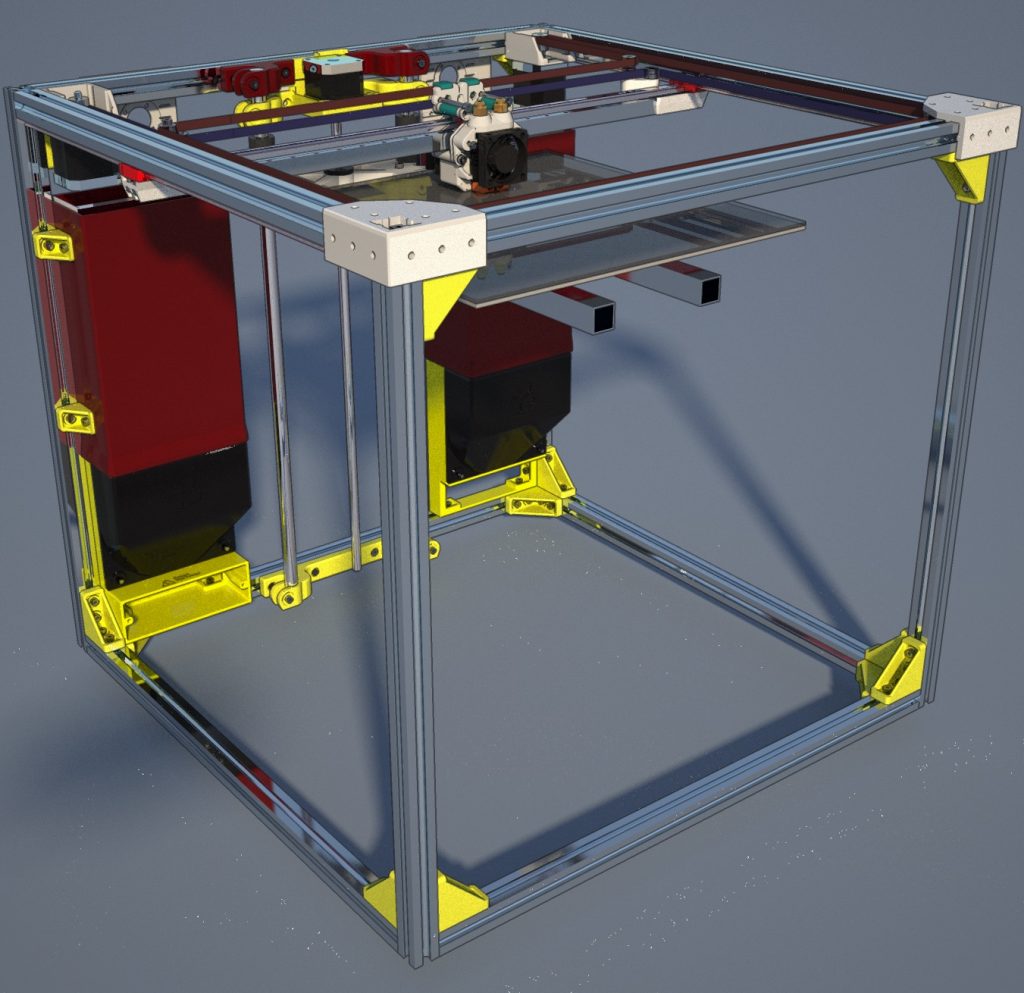
In the rendering shown above, all of the non-white and non-green plastic components are part of the revised configuration.
The overall CoreXY component of the current build is satisfactory and thus will be pretty much remaining the same, aside from the modified X axis support and some cosmetic revisions to the printed components.
by B Cantin | Jun 22, 2016 | Gemini 3D Printer
Work on the Gemini 3D Printer was on hold for a few months while I used it’s cart as a temporary plant nursery for my garden.
I created a few quick parts to get the bed mounted to the Z axis and get the machine up and running for some testing.
There have been a few print quality issues but they look to be mostly software tuneable items thus far. The machine has been able to print in both ABS and PLA.
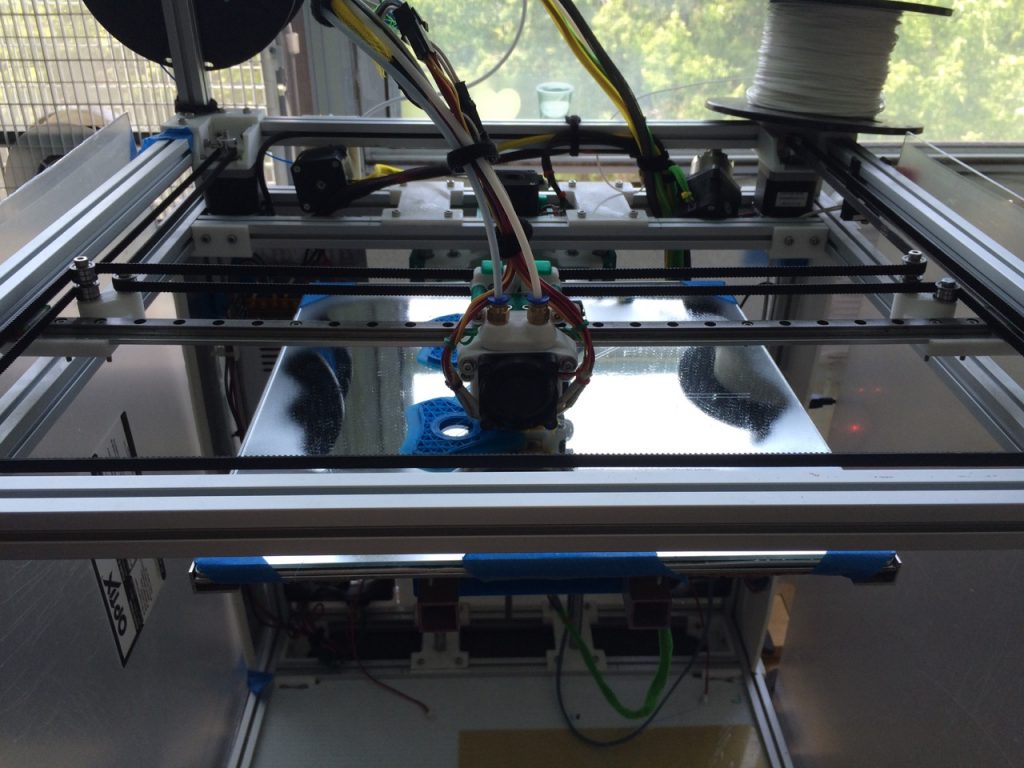
Gemini Printing ABS
Overall, I’m not as enthused with the final assembly of the prototype as I would hope to be – although I am excited to have the unit working so I can properly test the design out.
I believe I could make the machine more compact, easier to assemble and maintain, sturdier and still reach the basic print volume I am aiming for of 300mm X 300mm x 300mm+.
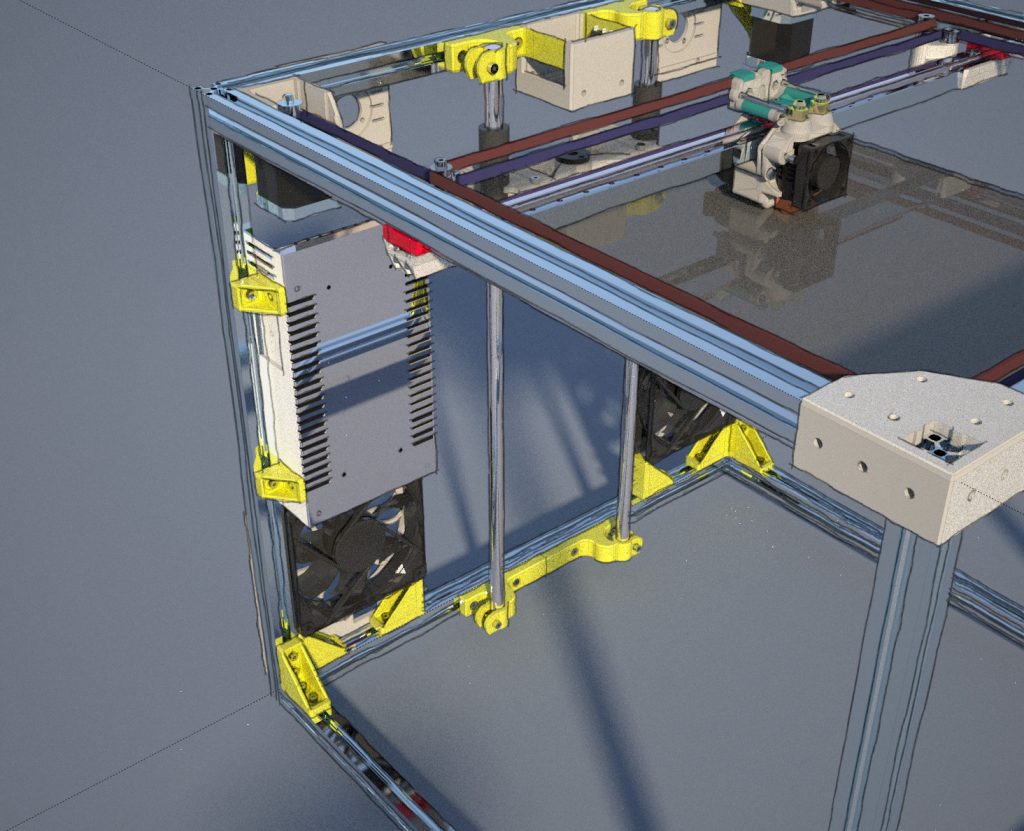
Partial artistic concept for revision 3.2.0
A quick bit of Sketchup work yesterday fleshed out how a rebuild of the rear of the printer could take shape.
by B Cantin | Mar 8, 2016 | Gemini 3D Printer, Kitchissippi-Delta
This linear carriage design is something I have been toying with for several years now.
It all started with having picked up a bulk lot of 608zz skate bearings with the intent of making a Rostock or similar delta printer some day, but mostly because I needed a few for my Mendel and at 30 cents a bearing for a hundred bearing I felt I couldn’t pass it up – I’d find a use for them.
I was actually working on the early proof of concepts for the K02 corexy printer I wanted to build when I came up with the idea of turning the square tubing 45 degrees. I had picked up some stock aluminum 3/4″ tubing at the hardware store to play around with and was trying to work out a simple method of utilizing them as both the frame and the linear guide using the skate bearings.
The main challenge was that the bearings need to be preloaded to an extent and most methods of getting them tensioned against the tube and constrained well enough to function as a linear guide required a great number of bearings. Such a mechanism gets quite large when dealing with skate bearings and typically requires less common bearings that are smaller.
I have no record of how long I spent just rolling bearings in various configurations along the aluminum stock and daydreaming until I stumbled across this trick, which I believe is unique to myself, of pinching an edge of the tube between two skate bearings to form a point on the linear guide. I recall that I printed various small plastic parts to test my various ideas which was an introduction to designing custom parts in SketchUp as well as proving the usefulness of rapid prototyping that can be achieved with a 3D printer. Any idea I had could be test implemented within a matter of minutes or at worst hours depending on the size of the part.
I quickly whipped up a linear carriage design that used three bearings mounted on a plate and a mirror of that held together with four bolts to form the linear carriage. I expanded on this and built a corexy stage with crude but workable filament drive made from reinforced fishing line.
This is an early prototype of the design, intended to be used with a CoreXY mechanism:
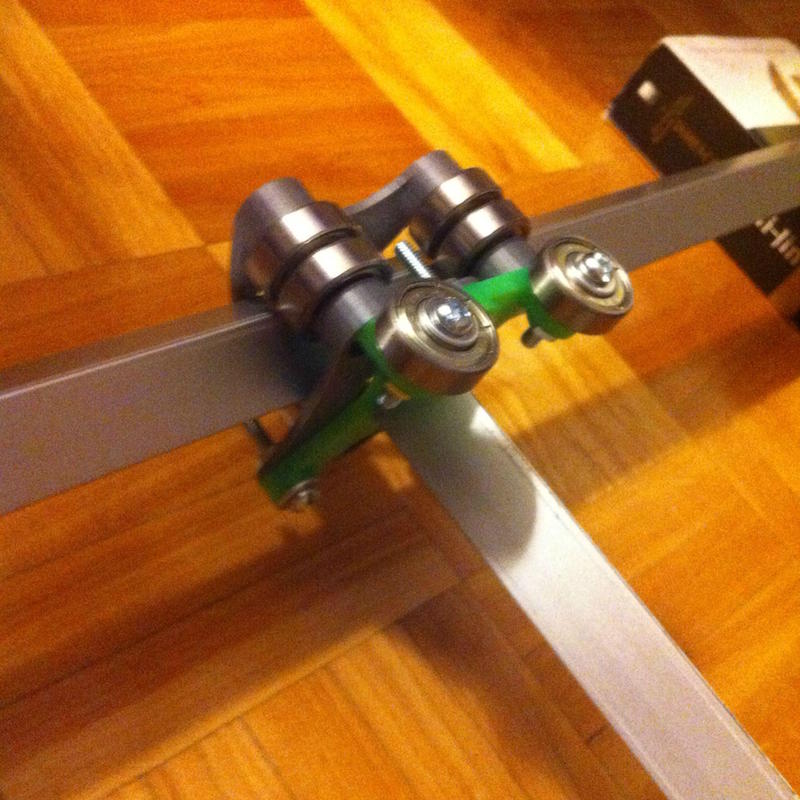
It worked fairly well and was able to plot out shapes reasonably accurate from g-code output from Slic3r. I had some initial concerns about the longevity of the soft extruded aluminum tubing verses the hardened steel edges of the skate bearings, as did those I shared the concept with on the #reprap irc channel.
After about 10 hours of running the mechanism it became apparent that the bearings tightened down to the point they’d be accurate linear mechanisms was eating deep gouges into the tubing and would need to be constantly tightened (by pulling the plates closer together) until there was going to be no tubing left.
Here is a picture of an early test build of the design:
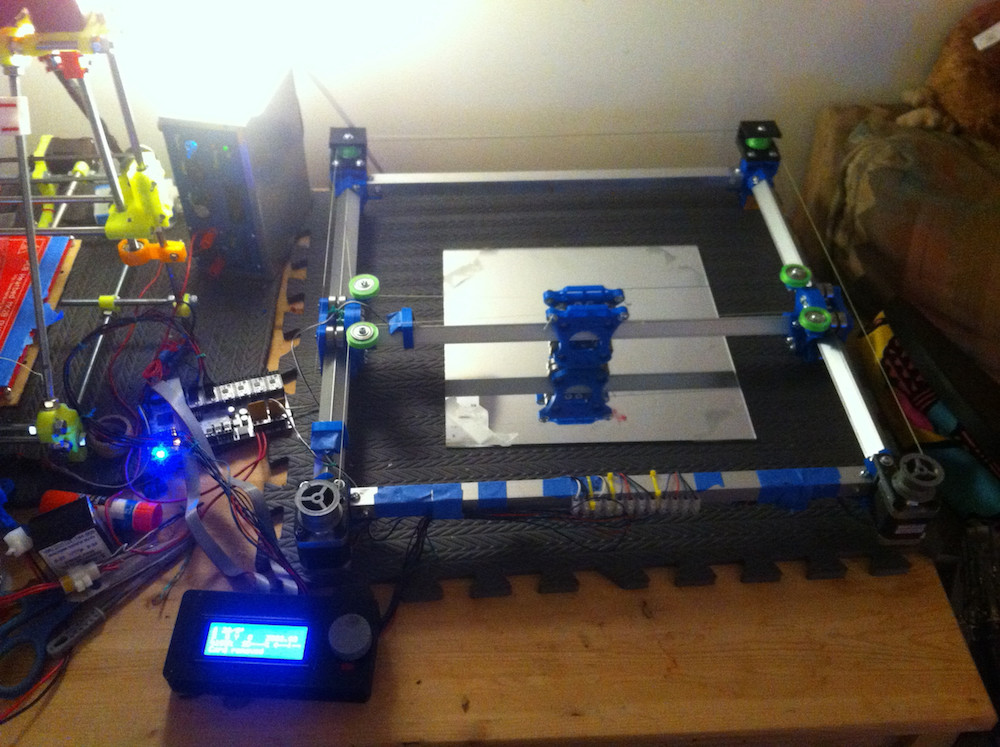
There are issues with the overall CoreXY mechanism shown, there are non parallel drive lines at the rear which would cause accuracy issues over the course of a print. It’s running on a RUMBA controller board and powered by my home made 12v lab supply, sitting beside an earlier build of my trusty Mendel. This is early in the testing and the aluminum tubing has yet to be eaten by the carriages. I’d already switched from a 3-per-side bearing system to a 4-per-side bearing system by this point to deal with binding issues caused by the stresses of the tensioned drive mechanism.
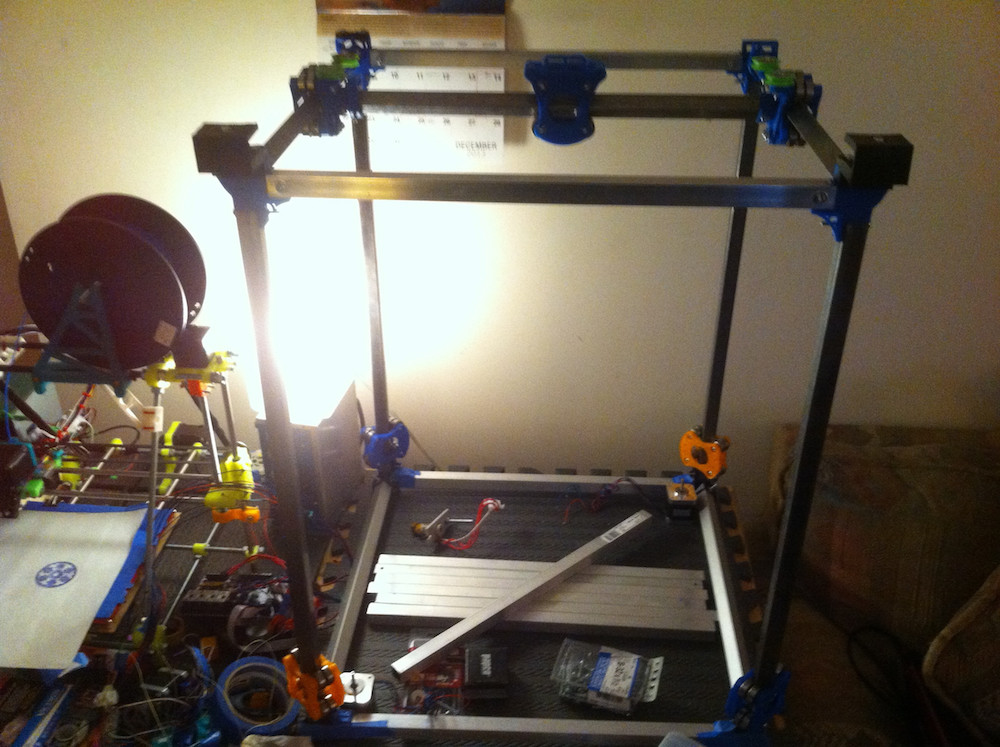
Work proceeded rapidly and by December of 2013 I had the above mechanism in place with steel tubes instead of aluminum on the moving axises and some ideas as to how to attempt a Z axis. The drawing on the piece of paper sitting on the Mendel’s bed was done by the steel version of the gantry and shows how much this concept dwarfed it.
I got so far as to mocking up a few Z axis designs for the CoreXY before I finally had to admit a bit of defeat that the moving weight of the carriages and the steel cross bar, as well as the Z axis variations were not going to meet my goals of a fast large format 3D printer. It worked, but it was going to be a slow machine – and I was not entirely convinced the simple filament drive system was going to be accurate without some serious reconsiderations. This project had started in late 2013 and I had started to question of the wisdom of filament drives in spring of 2014. GT2 timing belts were only just starting to flood the market, there were a lot of us playing with filament drives up to that point and running into certain concerns about positional accuracy with the windings on the spools. Timing belts were becoming cheap enough that the price was comparable to fishing line that was strong enough for RepRap usage and comes with easier repeatable motion.
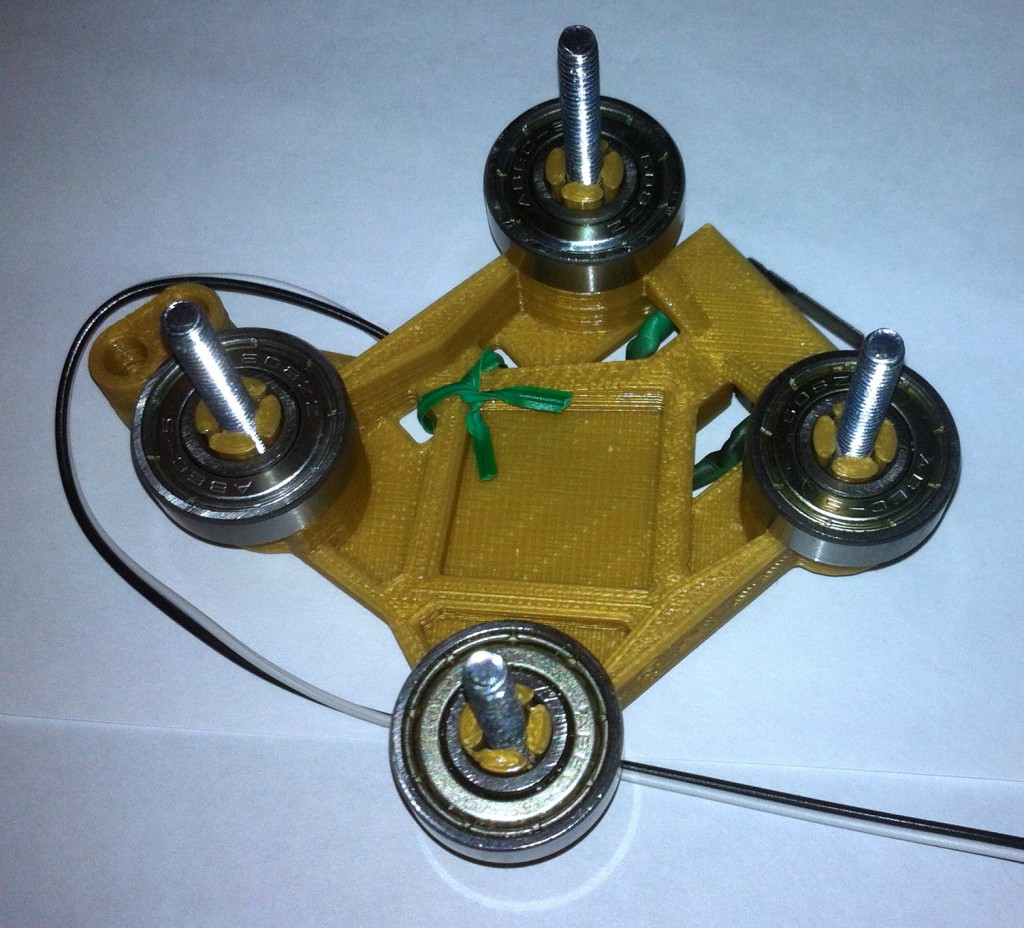
I had one last concept to try before I gave up on the big CoreXY machine – I wanted to make the carriages thin and remove the extra washers that I had been using as spacers between the two halves of the carriage. Above is a prototype of a snap-fit bearing holder system with an integrated end-stop and drag chain holder. This was not easy to design in SketchUp and I started to consider learning OpenSCAD around this time. The snap fit bearing holders were also a bust – the bearings really need to be constrained around their hubs from both sides in order to make this system work. Since it’s a unique concept, I wouldn’t have known unless I tried.
I decided there was going to have to be a better way to build a CoreXY printer, but thought the linear carriage would be particularly suited to a Delta style printer mechanism. Below is a side-by-side comparison of how the K02 mechanism became the K03 mechanism that I was using for the past 2 years. (right to left)
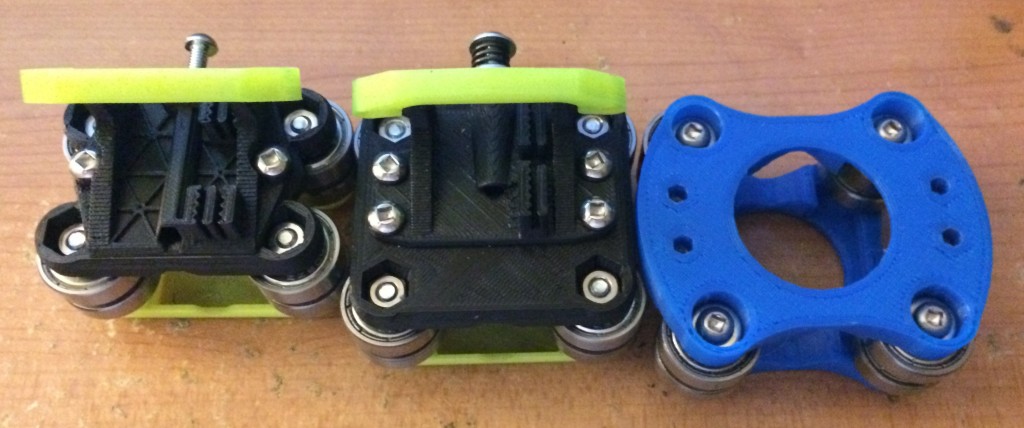
The final version on the left turns out to not be that final. It was an exercise in minimalism which carried onto my next project, the very first version proof-of-concept version of the Gemini 3D printer. Much like the first Gemini build, it proved that you can indeed building things too thin with plastic. The linear mechanism shown above did work for a time, but the printer ran into other problems and I got focused on other things, such as the Gemini.
It’s worth noting that the leftmost mechanism was still in place in the past week when I got the K03 Delta running again. Only the swivel and adapter portion were replaced.
by B Cantin | Jan 25, 2016 | Gemini 3D Printer
As I’ve discussed in my last couple of posts, I am redesigning the Z-Axis for the Gemini prototype.
The 12mm rods are now doubled up on each side and I am working on a test assembly which uses single LM12UU bearing per rod. From an ideal perspective, I should probably double up the bearings on the frontmost rod for each side.
Instead I am working on a test assembly which uses only one per side in order to make the mechanism shorter and optimize the achievable Z height for the printer.
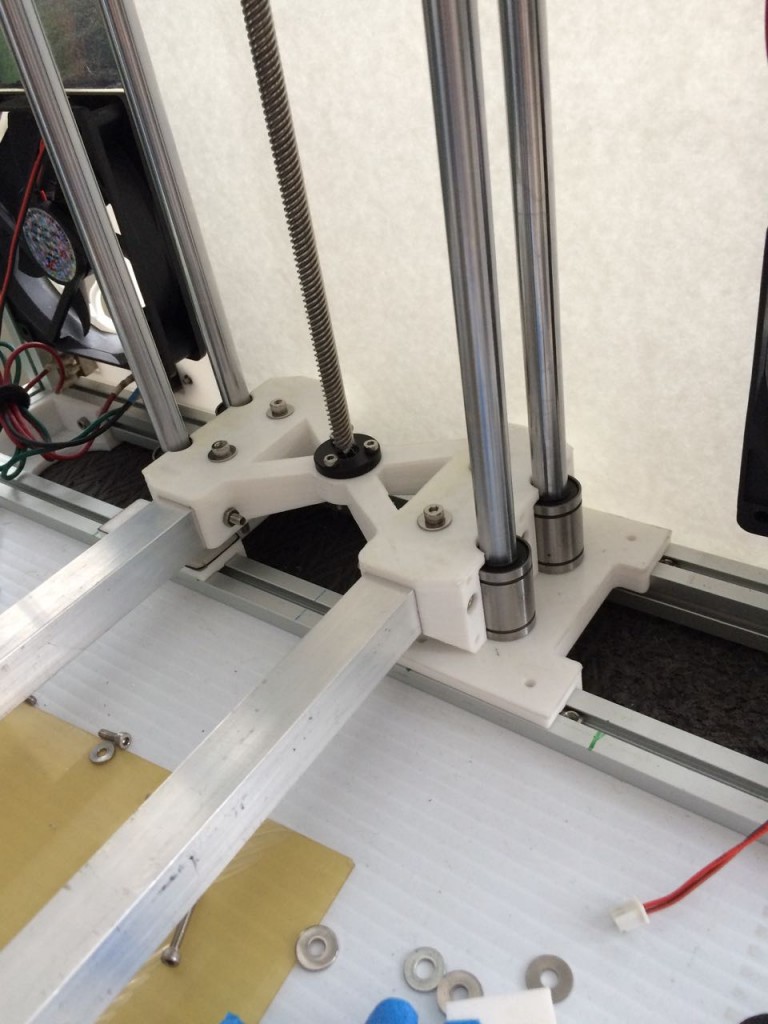
The above part was designed in OpenSCAD. The new build platform support arms are 3/4″ square aluminum tubes which have been drilled and bolted into the printed part using five M4x40 bolts per arm. There is no possibility of flex in either the arms or their bolt mount pattern of three across and two vertical.
Clamping blocks will be 3D printed and bolted onto each side using six M3x20 bolts per side.
Including the three M3x20 bolts which secure the leadscrew bushing to the part there are fifteen M3x20 bolts and ten M4x40 bolts required to hold everything together into a nice compact assembly.
Once I have the clamp parts designed, printed and attached, I can get the rod holders bolted down into their proper alignment and start testing the design for any sign of flex or binding when being driven by the motor. If all goes well then I will start on the design of the build platform mounts – they will be 3D printed and bolted to the support arms.
One thing to note is that with the above pictured reduced-height assembly design is that the leadscrew is not inside the bushing at it’s lowest position. If the assembly works as I hope then I can simply flip the Z motor mount upside down and re-mount the motor lower into the frame.
by B Cantin | Jan 20, 2016 | Gemini 3D Printer
In my last post I described some mistakes made in the Z axis design – particularly that I had not made a secure enough clamping setup on the LM12UU bearings and had also selected aluminum stock for the weight bearing arms that was not up to the task of supporting the build platform in a stable enough manner.
I have decided to correct this before proceeding with testing rather than waste my time fiddling with a clearly broken setup.
My general solution in the redesign is to overbuild the Z axis – this will remove any weight restrictions on the build platform (within reason, of course) and also allow the machine to move smoothly which should naturally translate into higher quality prints.
The second revision of the Gemini prototype used four 12mm hardened steel rods for the Z axis and moved the platform using two leadscrew motors in a similar vein to the RepRap Mendel Z axis with the difference being it used two guide rods instead of one on each side.
This design proved to be difficult to maintain level on the X plane due to the weight of the build platform and the ease at which a nicely machined leadscrew will turn. On the Mendel printers the nut-and-threaded-rod doesn’t turn turn easily with the limited weight applied to them and thus they do not tend to move on their own when powered down.
The third revision addressed this by using a cantilever design guided by two rods at the rear of the printer, leaving me with two spare 12mm rods. I am re-introducing them into the design by doubling up the linear rods on each side to create more rigidity on the axis.
I plan to replace the aluminum angle with 3/4″ square aluminum tubing which has much less flex, particularly at the lengths involved. The two square arms will be well constrained and might possibly lend itself to a three-point levelling system for the build platform as well.
I won’t have time tomorrow to work on this redesign due to other commitments, but I am attempting to get as much of it created today as I can and already have the lower rod holders being printed on my Prusa Mendel i2 as I write this.
Stay tuned, I will have pictures later this week and hopefully will be able to report some success.
by B Cantin | Jan 19, 2016 | Gemini 3D Printer
After wiring everything up and running electronics and motion testing, I am happy with with general design of the corexy system and the hotend mounting.
I ran the machine through some paces last night for several hours without any failures or signs of warping due to heat.
What was extremely disappointing was the Z axis and build platform mounting design – I had my doubts about this during construction and yesterday’s testing confirmed that there is a lack of rigidity in the whole setup. Getting the bed level is proving to be a large challenge given the amount of flex in the design.
I might be doing some more work to try to hack this into testing operation but ultimately it needs to be redesigned.
The heated bed platform is constructed using a standard RepRap heated bed which is bolted flush to an aluminum heat spreader and insulated on the bottom to retain heat. A 12″ x 12″ mirror tile from the hardware store provides a strong flat surface to extrude plastic onto.
It’s heavy. The base heating module weighs in at 970g and then jumps up to about 1620g once the mirror tile is added.
The net result of all that weight on the poorly designed LM10UU clamps and the skinny aluminium channel I used to hold it all up is a lot of flex and it’s very sensitive to vibration.
I plan to make a revised version with stronger bearing clamps as well as stronger support arms. I am seriously considering adding another 10mm thick linear guide rod or two to the design as well to enforce rigidity.
I’ll need to look at seeing what can be done to alleviate some of the weight if possible as well.
Otherwise, everything seems to be working well. There are a few more pieces which need to be added to the filament pushers so that it can actually start feeding plastic into the hotends but I don’t anticipate those will be too hard to design.
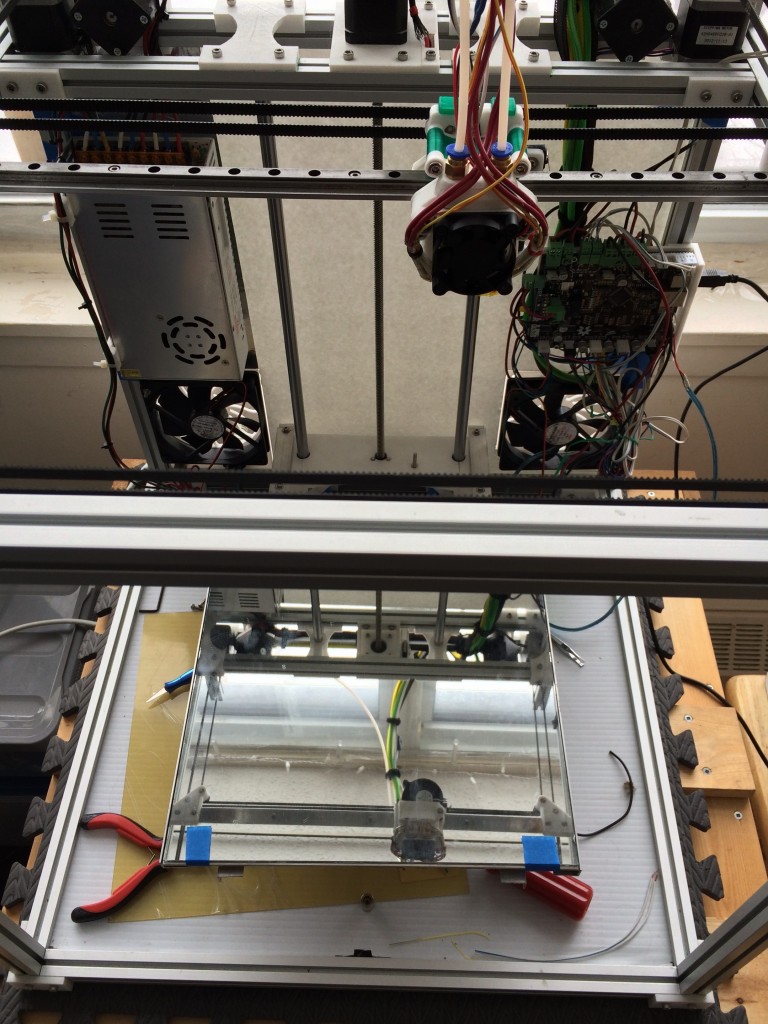
Update: I did a bit of disassembly on the build platform base – removing the glass bed guides from the assembly reduces the overall weight by 130g for a total of 1490g. Not really a significant savings overall in terms of performance of the current design. I might still try to press this into service in order to get the filament pushers finished and the printing abilities of this build tested. If I can get it printing some parts it may be easier to use the larger build volume (compared to my little Prusa Mendel i2) to create a new Z axis.
Recent Comments